Mastering FSMA 204 Compliance: A Strategic Guide for Food Industry Leaders
As the enforcement deadlines for FSMA Section 204 approach, food industry leaders have two big questions to consider:
- How are we going to address new compliance requirements?
- How will we do so without experiencing significant disruption to their operations?
We’d suggest a third question: How can we create more efficient operations during the process? This opportunity is often overlooked but can be an unexpected benefit of compliance.
These efforts can create long-term benefits like optimizing resource management and advancing your sustainability goals.

How to get from here to there: 5 Steps to mastering FSMA Section 204 compliance
Meeting FSMA 204 compliance obligations goes beyond ticking off checklist boxes. To meet new standards, you need a structured, forward-thinking game plan that strengthens your supply chain and builds consumer trust through transparency and reliability.
1. Step up your traceability systems
Traceability is at the core of FSMA Section 204. However, many businesses aren’t quite there yet when it comes to implementing tools to meet FSMA 204 obligations.
While barcodes have served the industry well for inventory management, they’re limited by issues such as data capacity, security, and physical proximity. They also only provide “moment in time” tracking upon scan, whereas FSMA requires active tracking, which is available at any place and at any time along the supply chain.
New advanced traceability systems—such as IoT-enabled tracking devices—can help businesses build more efficient processes while facilitating FSMA requirements.
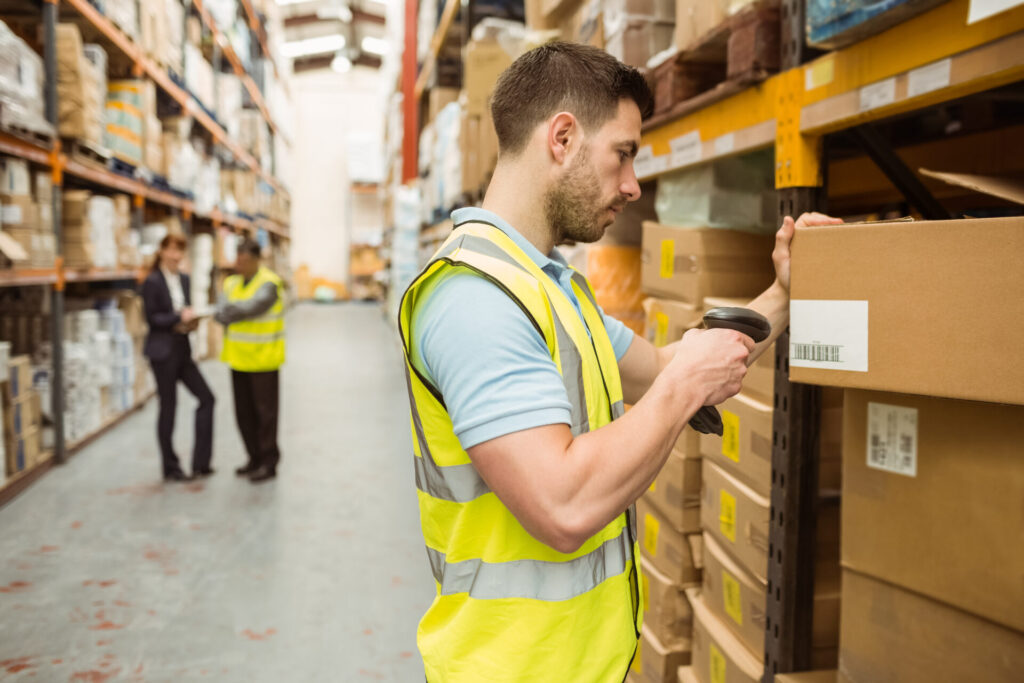
Strategic approach:
Digitize and automate: Manual scanning and measuring processes simply can’t meet the rigorous obligations of FSMA 204s, and relying on them risks errors that could cost you. Automation is the smarter choice—it captures key data elements (KDEs) during critical tracking events (CTEs), effectively reducing labor demands without compromising data quality or the delivery of high-quality products.
“Internet of Things” or IoT-system: IoT can be a key way to automate data collection. The “things” are any combination of physical trackers on the products or shipping containers, data transmission capture points, reporting dashboards, and infrastructure, like cell towers.
With IoT-enabled solutions, businesses capture real-time environmental data like temperature and humidity. These features allow leaders to take immediate corrective actions if deviations occur, and they also vastly simplify data logging.
Integrated systems: When data is scattered across multiple sources, it slows access to important information, makes reporting more difficult, and increases the chance of mistakes. Combining these systems lets businesses automatically share information across the supply chain, reduce repeated work, and ensure every detail is recorded and readily available.
End-to-end traceability systems can capture and share key data elements (KDEs) at each critical tracking event (CTE), allowing communication between partner platforms throughout the supply chain.
Actionable directive: Rigorously audit your current systems – those within your company’s supply chain nodes and those within your supplier or retail partner. Once you know where your gaps are, invest in IoT and cloud-based solutions to help bridge them and create better supply chain visibility.
2. Make partnerships a top priority
FSMA 204 mandates collaboration across the supply chain—and your compliance is only as strong as your weakest link. This makes partnerships a top priority. The goal is to create a unified and reliable data exchange framework to ensure consistent compliance across all levels.
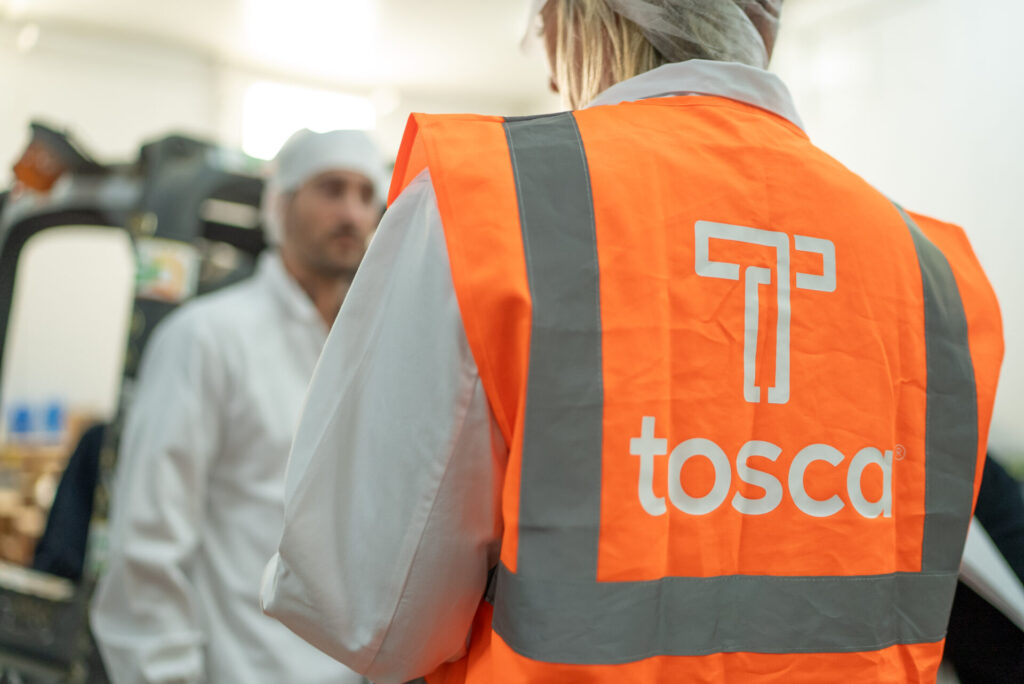
Strategic approach:
- Standardize data protocols: Work with suppliers to implement a standard set of KDEs. When you work within consistent standards, you set the conditions for smooth data transfer while mitigating the risk of compliance failures.
- Implement auditing and training: Establish a rigorous supplier auditing program to verify compliance readiness. Provide joint training sessions for your team and partner businesses on FSMA 204 requirements and expectations.
- Tech-driven collaboration: Don’t let outdated communication methods throw a wrench in the works. Modern platforms, like Tosca’s Hub, help businesses communicate better with suppliers while supporting traceability programs and coordinating logistics more efficiently.
Consider getting involved in initiatives like the Partnership for Food Traceability, which is working to address the implementation challenges of FSMA 204. These collaborations can provide valuable insights as your business meets these new compliance requirements.
Actionable directive: Suppliers should develop standardized data protocols and participate in joint training sessions. Distributors need to focus on integrating systems for seamless data transfer. Retailers must establish clear compliance expectations and provide feedback to their supply chain partners.
3. Get strategic with your asset management
By having a plan for asset management, businesses can put themselves on the path to easier FSMA compliance.
Asset management allows for more precise traceability, data collection, and food safety practices. Think real-time product tracking, increased data integrity, and quickly identified food safety issues—all of which give your business serious practical advantages in your day-to-day operations.
Beyond compliance, effective asset management also encourages sustainability with longer lifecycles for assets and reduced single-use packaging waste in the supply chain.
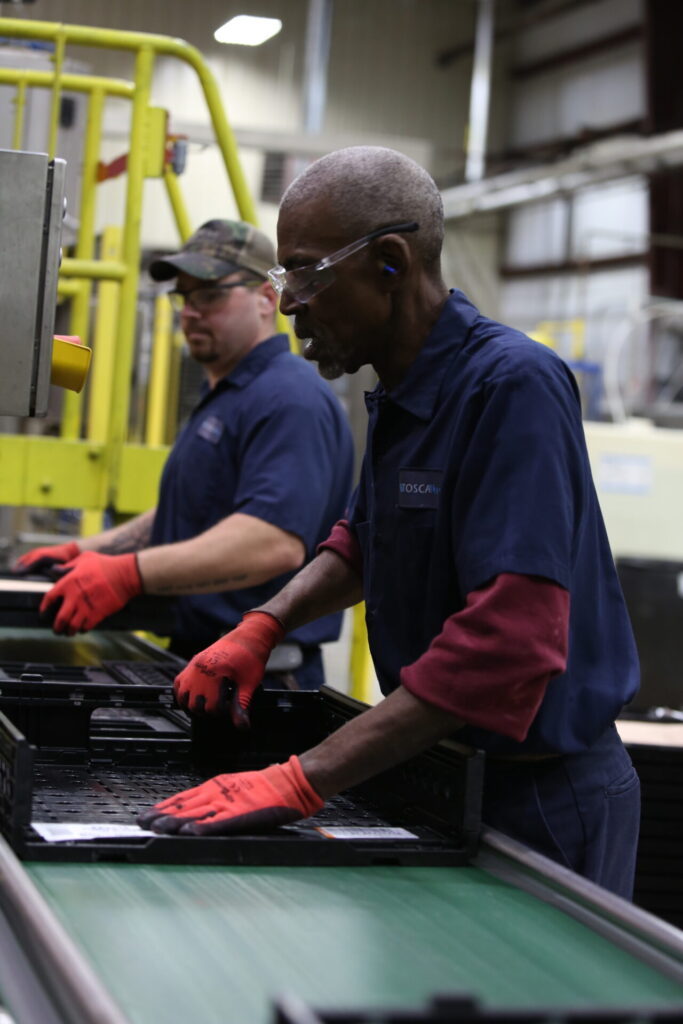
Strategic approach:
- Leverage RFID and sensor technology: Technology-enabled reusable packaging delivers real-time asset location and condition data. With this information, businesses can minimize shrinkage and avoid non-compliance due to mishandling or temperature fluctuations.
Depending on your business needs, you can leverage either passive or active tracking solutions. Passive tracking tools, such as RFID-equipped crates, provide detailed location and asset data at critical tracking events (CTEs). Active tracking tools go a step further, continuously monitoring environmental conditions like temperature and humidity to ensure product quality and compliance with FSMA requirements.
- Adopt a circular pooling system: Circular pooling systems can optimize your supply chain by reducing waste and introducing efficiencies, but those aren’t the only benefits. You’ll be able to access shared resources. For example, businesses that use Tosca’s reusable packaging solutions can tap into our R&D initiatives.
- Lifecycle monitoring: By logging the age, usage history, and maintenance records of reusable assets, businesses can get proactive about replacing or repairing items before they jeopardize food safety or traceability.
As you implement new traceability systems, it’s important to find solutions that allow for interoperability and facilitate meeting FSMA 204’s 24-hour response time requirement.
Actionable directive: Conduct a comprehensive audit of your current asset management practices to spot traceability gaps. Once you know where the gaps are, build an action plan with the next steps. Running a pilot program with IoT-enabled reusable packaging in a specific product line or with a key supplier can validate the ROI of advanced asset management.
4. Enhance your sanitation standards
Food industry businesses have long prioritized ensuring safe and sanitary conditions for food and workers. However, FSMA 204 requirements are set to expand on this priority, requiring detailed records of sanitization processes throughout the supply chain to prevent contamination, protect food safety, and allow for full traceability.
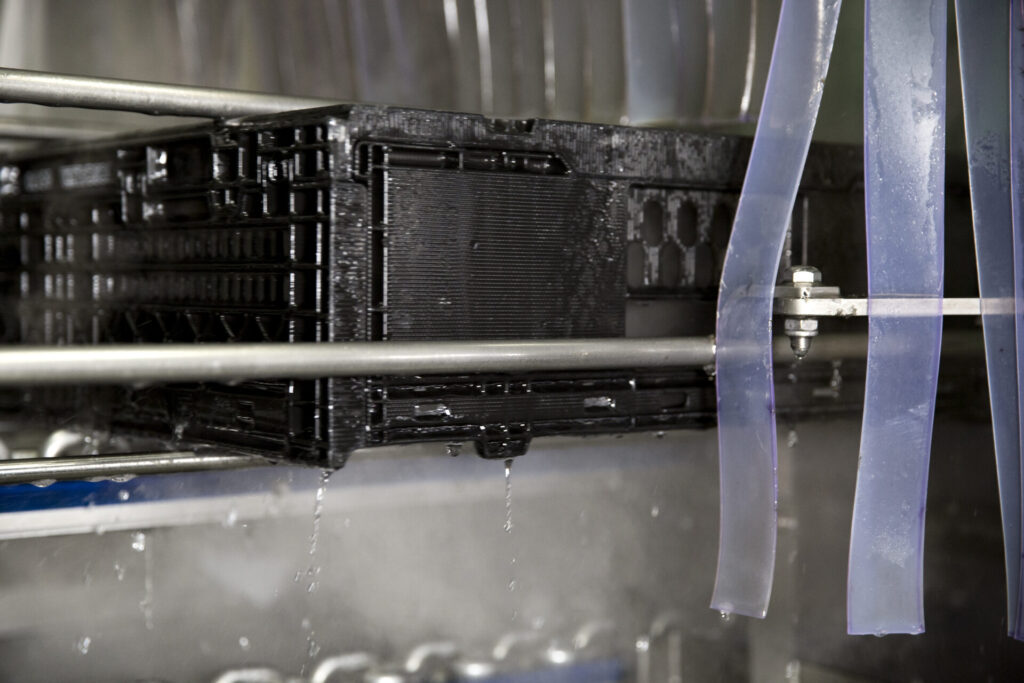
Strategic approach:
- Invest in packaging systems that enable automation. Automated cleaning and inspection systems help keep products safer and minimize the risk of cross-contamination.
- ISO-certified cleaning processes: When using reusable packaging, it’s key to work with vendors with ISO 22000-certified wash centers, ensuring comprehensive sanitization. Tosca’s network of wash centers leads the industry in cleanliness and compliance.
- ISO-certified cleaning processes: When using reusable packaging, it’s key to work with vendors with ISO 22000-certified wash centers, ensuring comprehensive sanitization. Tosca’s network of wash centers leads the industry in cleanliness and compliance.
- Document, document, document: Keep meticulous records of all sanitation activities, including methods, frequency, and outcomes. These records must always be audit-ready.
Effective sanitation practices significantly reduce the likelihood of recalls and encourage a more resilient and trusted food supply chain—but they also strengthen your brand reputation.
Actionable directive: Conduct a gap analysis of your current sanitation protocols. Upgrade to automated systems if needed and ensure your processes are fully aligned with FSMA standards.
5. Utilize data analytics for proactive management
Information on inventory, environmental conditions, sanitation, supplier compliance—the list goes on.
FSMA 204 compliance generates a huge amount of data. Organizations that use this data will gain a significant competitive advantage as they anticipate supply chain issues, refine their internal workflows, and create data-driven strategic plans.

Strategic approach:
- Analyze for insights: Use advanced analytics to interpret traceability data. Pinpoint patterns, optimize logistics, and spot potential compliance issues in advance.
- Streamline bookkeeping: Understand your numbers better. FSMA 204 compliance data can significantly improve financial record-keeping. With financial data, you can more precisely allocate costs, value inventory, and manage financial reporting.
- Guide inventory management: Traceability data can also refine inventory practices, minimizing shrinkage and maximizing shelf life. Use this data to inform procurement and storage decisions.
- Plan for future regulations: Stay one step ahead of evolving standards by using traceability data to build predictive models. This will prepare your organization for regulatory changes and position you as an industry leader.
Data analytics can be the difference between confusion and clarity. With deep information at your fingertips, you can anticipate and shape industry trends rather than reacting to regulatory changes.
Actionable directive: Advanced analytics can allow better collaboration across the supply chain and with partner organizations. Working with traceability technology providers, pooling service experts, and supply chain experts, businesses can build unified systems.
For example, IoT-enabled platforms capture real-time environmental conditions and share KDEs with necessary parties. By operating within one data ecosystem, it’s easier to provide suppliers, distributors, and retailers with the data they need to address audits, avoid regulatory fines, and maintain uninterrupted product flow.
Tosca’s strategic solutions for FSMA 204 compliance
With Tosca, you can simplify FSMA compliance requirements and create operational advantages for your business. Here’s how our solutions make a difference:
- IoT-enabled reusable packaging: Our RFID-equipped crates and pallets track location and environmental conditions in real time, seamlessly capturing KDEs during every CTE.
- Data & ordering hub: A fully integrated platform that ensures smooth data exchange and enhances supply chain transparency.
- ISO 22000-certified wash network: Industry-leading sanitation standards to prevent cross-contamination and uphold food safety.
- Efficient pooling systems: Automated tracking and clean, reusable assets that optimize operations and protect product quality.
Tosca’s team of experts is equipped to guide you through every step, from initial assessments to full-scale implementation.
Get an expert supply chain analysis to future-proof your supply chain and achieve FSMA 204 compliance with confidence.